产品目录
液体涡轮流量计
液体流量计
水流量计
油流量计
气体涡轮流量计
椭圆齿轮流量计
电磁流量计
涡街流量计
蒸汽流量计
孔板流量计
旋进旋涡流量计
热式气体质量流量计
转子流量计
浮子流量计
靶式流量计
气体流量计
超声波流量计
磁翻板液位计
浮子液位计
浮球液位计
玻璃管液位计
雷达液位计
超声波液位计
投入式液位计
压力变送器
差压变送器
液位变送器
温度变送器
热电偶
热电阻
双金属温度计
推荐产品
联系我们
- 金湖凯铭仪表有限公司
- 联系电话:15195518515
- 在线客服:1464856260
- 电话:0517-86801009
- 传真号码:0517-86801007
- 邮箱:1464856260@qq.com
- 网址:http://www.bubu8.com
- 地址:江苏省金湖县理士大道61号
涡轮流量计在液氧煤油流量测量的应用
发布时间:2020-08-30 23:05:48 点击次数:2113次
摘要:以涡轮流量计在液体火箭发动机试验中的应用为研究对象。针对液氧煤油发动机试验中流量测量数据出现的异常波动和较大的系统误差,从涡轮流量计的现场使用状态进行了分析。认为解决的方法是用分节式电容液面计对涡轮流量计进行真实介质的校验,校验的方法可通过液面计测得的体积流量反算出涡轮流量计的流量系数来实现。
1、引言
液体火箭发动机试验中,推进剂流量是关键参数。采用的测量装置多为涡轮流量计。涡轮流量计有许多优点:精度高(5‰),重复性好,滞后时间较小,耐压和选用温度范围较宽。与其他类型的机械式流量计相比,在相同的量程下,体积较小、易安装。但是,由于它是一种速度型的容积仪表,对管道中流态的变化很敏感,再加上涡轮流量计校验介质(水校)与试车介质的不同,以及使用状态与校验状态的不同,容易引入系统误差。特别在低温推进剂流量测量中,其介质的低沸点和可压缩性,使得准确测量变得复杂和困难。
2、法兰夹装式液体涡轮流量计工作原理及主要特性
当流体经过涡轮流量计管内腔时,推动带有螺旋叶片的转子旋转,叶片周期性的改变信号发生器磁路的磁阻,使通过感应线圈的磁通量发生周期性的变化,从而感生一个与电流成正比的交流信号,通过测量传感器输出信号频率达到被测量流体流量的目的。
如果涡轮上的叶片与涡轮轴线的夹角为α,当流体通过时,就有一个力作用在叶片上,这个力与流量、流体的密度及流速有关。则涡轮转速n与体积流量Q的关系推导如下:
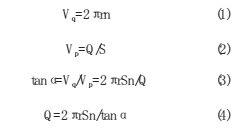
式中,r为叶轮平均半径;Vq为平均半径r处流体的切向流速;n为涡轮转速;Vp为轴向平均流速;S为叶栅的流通截面积;Q为体积流量。
由式(4)可知,当涡轮结构一定时,r、s、α为定值,tgα为常数,则转速n与Q成正比。
以上结论是在忽略涡轮转动过程中机械摩擦和各种阻力下导出的,但实际应用中,流量与涡轮转速之间并不能维持上式那样简单的线性关系。在流量较小时,转速与流量之间不是线性关系,这主要是由于在低流量下流动阻力变化较大;当轴承摩擦力矩小到可以忽略时,流量计转换系数可看作常数,此时流量计工作在紊流状态,流量与转速将维持线性关系;当流量较大时,特性迅速改变,这是因为流量过大,叶轮转速变快,流体的相对流速对涡轮轴线的夹角更接近叶片的倾角,减小了流体对叶片的冲击作用,加上叶片顶与外壳之间的间隙造成的漏流量随着流速增加而增大,改变了流量计的转换系数,破坏了Q与n的线性关系。
3、影响涡轮流量计在火箭发动机试验中的主要因素
涡轮流量计的测量精度受安装地点、环境、流体的特性、上游流动情况、流体温度、压力、流体粘度及流体清洁度的影响和制约。
涡轮流量计对入口的流速分布*敏感,入口流速的突变和流体的旋转使得测量精度下降很大。在工程测量中,往往由于直管段长度不够,或水平安装角度过大或流量计附近管道内所使用的各种密封垫突出等原因,使进口处流体的旋转未能彻底消除,而改变了流体和涡轮叶片的角度。这种影响一般会使精度变化2%左右。在液体火箭发动机试验中,以下几方面对涡轮流量计测量精度的影响是主要的。
3.1安装状态
按涡轮流量计的使用要求应安装在便于维修并尽量避免管道强振动、强磁场和热幅射的位置。发动机热试车时,强振动、磁场及热幅射始终存在。目前,国内外对振动和热幅射引起涡轮流量计测量变化范围尚无结论。对于磁场带来的干扰,可以通过测试电缆的屏蔽一点接地得到有效的解决。
涡轮流量计校验和使用时都要求水平安装。且尽量按照校验时的状态安装。安装状态不同,摩阻就不同,摩阻又称阻尼力,由轴承的磨擦阻力和信号发生器的电磁的阻力组成。其中,轴承的磨擦阻力是主要的。经试验证明,轴承受力变化会造成流量(系数)的波动,从而造成 2‰左右的误差。在小流量时,其影响更大。 摩阻不同,同**量下涡轮转速也不同。
3.2入口直管段的设置
入口直管段的长度对涡轮流量计的测量精度影响很大,其直管段长度的设置可按下式计算:

式中,L为入口直管段长度(直管段内径应与流量变送器内径相同);D 为变送器的内径;f为管道内摩擦系数,紊流状态时f=0.0175;k为漩涡速度比,由流量计的前管路情况确定。
k的取值,一般为:
k=0.75(流量计前有同心收缩管);
k=1.0(流量计直管段前有一个圆弧弯头);
k=1.25(流量计前有同一平面的两个弯头);
k=2.0(流量计前有不同平面的两个弯头);
k=1.0(流量计前有全开阀门);
k=2.5(流量计前有半开阀门);
k=2(流量计前有直角湾头)。
由式(5)可计算出涡轮流量计在校验和使用时配套直管段的量小长度(见表1):
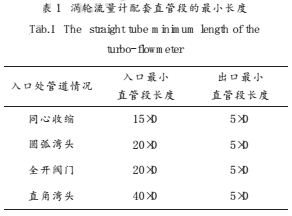
发动机试验时,由于涡轮流量计安装位置所限,其入口、出口无法完全满足上述条件。按校验时经验数据,一般认为:在涡轮流量计入口、出口分别安装20×D和5×D长的直管段即可起到有效整流的作用。
3.3流体温度
流体温度变化会引起涡轮流量计金属材料热胀冷缩,几何尺寸也随之变化,因而引起转速的变化。叶轮转速随温度变化呈线性变化。经试验证明,夏季校验的流量计在冬季使用时造成的误差可达0.2%(温差达 50℃时)。对于用低温测量的流量计(常温水介质校验)则影响更大。
4、流量测量数据的异常
在某试车台液氧/煤油试验中,液氧和煤油系统均在主管路上串联安装双涡轮流量计,并在泵前安装了*三个流量计(液氧系统流量计口径为300mm,煤油系统流量计口径为200mm)。但热试车稳定段中流量测量数据波动较大。如在液氧稳定段流量测量中,氧泵前流量计波动在20kg以内,液氧主管道1位置波动在9kg以内,氧主管路2位置波动在8kg以内。煤油泵前流量计上下波动在4.5kg以内,煤油主管道两个流量计上下波动均在3kg左右。除了流量计自身波动较大外,主管道两个流量计在稳定段下测得的平均值也有较大差异(泵前流量计受安装环境所限,不做探讨):液氧主管路两个流量计测量差值为2.5~5.0kg/s,煤油主管路两个流量计测量差值为1~3kg/s。
4.1主管道流量计测量数据的差异
稳定段下主管道两个串联流量计测量平均值的差异是系统误差,这主要跟每个流量计的性能有关,但也跟安装位置(入口直管段长度及阻流件情况)和安装状态有关,因为两个位置处流体的旋流情况、阻流件情况以及流量计入口流速分布均匀度有一定差异。另外,按水平位置校验的流量计,若使用时安装倾角过大,轴承的摩擦阻力将变大,流量测量值将偏小。经定位试验验证:若倾角超过5.0°,对测量精度有影响(某试车台液氧主管道水平倾角为5.8左右)。
除了上述影响外,校验时为单台校验,而热试车时为串联使用。认为位置1处的流量计对位置2处的流量计的测量值是有一定影响的,因为介质通过位置1流量计后是高速旋流状态,在进入位置2流量计(前直管段若小于20×D)入口时旋流无法完全消除。可以肯定流速越高旋流越严重,对位置2流量计的影响也就越大(某试车台液氧主管道位置2流量计入口直管段长度为16×D,煤油位置2流量计入口直管段长度大于20×D)。
4.2测量数据的波动
由于液氧和煤油泵前流量计安装位置受直管段长度等因素的限制,以及流量计输出波形的不正规,测量数据存在较大的波动是可知的。在影响其诸多的因素中,根据现场使用状态来分析,*先,安装位置除受直管段长度影响外,流量计本身输出波形的脉冲宽度不一样,单周期测量时会引起较大波动;其次,主管道水平倾角过大也是影响流量计测量数据波动的一个原因。理由是:涡轮流量计使用和校验时都要求轴向要平衡。由于倾角过大,涡轮流量计在工作时轴承将不能保持动态平衡,会使轴承摩阻发生变化,引起流量(系数)的波动。其后果导致测量数据波动大。
从试验数据分析可知,煤油是常温测量,测量的精度远高于液氧,其测量差异可通过修正方法基本消除。而液氧流量测量是在低温和高压状态下进行的,液氧的低沸点和可压缩性,使得准确测量其密度又成为一个难题。另外,涡轮流量计是常温水介质校验,而用于低温液氧测量时,认为会使其轴承、叶轮等金属材料不同程度的冷缩,结果会使流量(系数)发生一定的变化。
发动机试验流量测量,*关心的是稳定段的流量测量。理论上讲,如果流量计使用状态和校验时的状态完全一致,系统误差是可以消除的。但发动机热试车时的环境恶劣,无法完全满足这一条件。在现有的使用状态下提高其测量的精度成为亟待解决的课题。认为解决的方法是用分节式电容液面计对涡轮流量计进行真实介质的现场校准。
试验台液氧容器装有分节式电容液面计(精度3‰),可测平均流量。分节式电容液面计一方面可以做为流量测量手段;另一方面,在试验中可做为涡轮流量计的校验标准。试验中,只要液面计准确测得某平稳段的推进剂体积流量,就可通过对应时间内测得的体积流量以及对应时间内流量计输出的脉冲数反算出流量计的校准系数。几次试验数据积累后,可用*小二乘法拟合出一条曲线,准确的给出现有使用状态下涡轮流量计的校验系数。
5、结论
(1)认为涡轮流量计的安装状态、直管段设置、流体温度是影响涡轮流量计测量精度的主要因素。
(2)针对液氧/煤油发动机流量测量数据的异常,根据现场使用状态,分析并指出影响其测量精度的主要因素。提出了用分节式电容液面计对涡轮流量计进行真实介质的现场校准。现场校准的好处一是可以在不改变现有使用状态下基本消除系统误差;二是涡轮流量计不用再进行水校,降低了试验成本。
相关资讯
- 气体涡轮流量计安装直管段要求
- 气体涡轮流量计的结构与工作原理
- 气体涡轮流量计的产品特点和适用范围
- 气体涡轮流量计选型指南与外形尺寸
- 涡轮流量计的常见故障及排除
- 涡轮流量表怎么调节
- 涡轮流量计安装直管段要求
- 涡轮流量计的适用场合与量程范围
- 涡轮流量计由什么组成
- 涡轮流量计的工作原理
- 压力对涡轮流量计精度的影响
- 液体涡轮流量计使用常见问题
- 液体涡轮流量计的使用场合
- 液体涡轮流量计怎么接电
- 涡轮流量计的使用范围
- 涡轮流量计安装条件与环境要求
- 涡轮流量计安装在什么位置
- 液体涡轮流量计设置方法
- 气体涡轮流量计使用环境
- 气体涡轮流量计使用注意事项
- 气体涡轮流量计怎么清洗
- 气体涡轮流量计适用范围
- 气体涡轮流量计为什么要加油
- 气体涡轮流量计波动大解决办法
- 气体涡轮流量计安装距离要求
- 气体涡轮流量计安装注意事项
- 气体涡轮流量计应用范围
- 气体涡轮流量计常见故障有哪些
- 提高气体涡轮流量计精度的方法
- 气体涡轮流量计精度等级