产品目录
液体涡轮流量计
液体流量计
水流量计
油流量计
气体涡轮流量计
椭圆齿轮流量计
电磁流量计
涡街流量计
蒸汽流量计
孔板流量计
旋进旋涡流量计
热式气体质量流量计
转子流量计
浮子流量计
靶式流量计
气体流量计
超声波流量计
磁翻板液位计
浮子液位计
浮球液位计
玻璃管液位计
雷达液位计
超声波液位计
投入式液位计
压力变送器
差压变送器
液位变送器
温度变送器
热电偶
热电阻
双金属温度计
推荐产品
联系我们
- 金湖凯铭仪表有限公司
- 联系电话:15195518515
- 在线客服:1464856260
- 电话:0517-86801009
- 传真号码:0517-86801007
- 邮箱:1464856260@qq.com
- 网址:http://www.bubu8.com
- 地址:江苏省金湖县理士大道61号
涡轮流量计在线运行工况评估标准与流量计分析
发布时间:2020-11-26 07:59:50 点击次数:2275次
摘要:在建立流量计工况流量评估模型和计量风险预警模型基础上,运用远程监测系统对T-商用户涡轮流量计运行工况进行量化评估,提出了提高流量计计量准确度、减小燃气供销差率的措施。
1、概述
伴随着科技进步和能源消费水平的不断攀升,工商用户用气设备、用气负荷日趋复杂多样。工商用户流量计(以下简称工商大表)作为用气现场唯的贸易结算计量器具,如何掌握它的运行工况信息,及时发现计量故障,纠正用户违章用气行为,一直是燃气经营者关注的大事。
燃气工商大表远程监测系统是近年发展起来的、针对工商业用户燃气计量和压力、温度数据进行采集监测和分析的系统。该系统可**了解在用流量计、燃气设备的运行状况,包括燃气温度、燃气压力、瞬时流量、累计流量等,通过实时采集数据,为及时发现计量故障、减少供销差率,提供先进的信息技术工具。
西安秦华天然气有限公司工商大表远程监测系统于2011年12月25日完成了100台涡轮流量计数据传输单元(DTU)的软、硬件安装。系统规定,DTU终端每2min采集1次数据,通过无线GPRS上传服务器,系统自动生成流量、温度、压力变化曲线,并具备数据异常报警功能。
2、在线评估目的
按照相关技术标准,影响在用脉冲输出涡轮流量计计量准确度的因素有很多,涉及到诸多业务方面。涡轮流量计在线评估目的*先是运用信息技术工具,掌握在用的涡轮流量计运行工况信息,及时辨识计量风险,避免气量损失;其次分析现阶段影响涡轮流量计计量准确度的主要原因,总结经验,为提高相关业务管理水平打下基础。
3、涡轮流量计在线运行工况评估标准
在规定的数据采集时间里,以系统采集的每台流量计瞬时工况流量qg出现在(20%~90%)qmax(qmax为流量计*大计量工况流量)计量区间频数累加和,与(0~100%)qmax频数(不含工况流量qg为0的频数)累加和之比为主要判别依据,压力传感器、温度传感器采样值为辅助评估依据。
评价一台涡轮流量计运行工况好与坏的具体标准主要有以下两方面:
①流量计工况流量qg能否随用户用气负荷变化保持在(20%~90%)qmax计量区间内,以确保计量精度。
②流量计体积修正仪能否将工况流量qg,精确地转换为贸易结算值(标况体积)。这一点对于智能体积修正仪,更加依赖温度、压力传感器测量稳定性。
4、工况流量评估与计量风险预警模型
4.1工况流量评估数学模型
根据上述评估标准,在假设工况流量qg﹥0的条件下,建立如下模型:
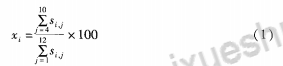
式中 xi———*i台流量计的评估得分
si,j———*i台流量计工况流量qg在j区间内出现的频数
j———流量区间编号,定义见表1
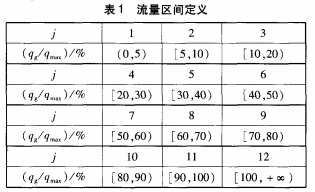
4.2工况流量评估数学模型的局限性
系统规定,生成的工况流量qg频数在流量区间边界取下限、不取上限。例如,当qg=5%qmax时,即为qg∈[5%qmax,10%qmax)。当用户不用气,工况流量qg=0时,系统生成频数也将全部落在(0~5%)qmax区间内。这样将使评估模型失去意义,技术人员删除了所有工况流量qg=0的系统频数。模型只适用于工况流量qg﹥0的条件。因此,在使用该模型时有以下限制:
①有效性限制。当用户用气流量始终小于流量计始动流量,或流量计涡轮被阻无法旋转时,工况流量qg将为0,致使模型无法评估。
②时效性限制。模型评估成绩只能表征这台流量计在评估时间段内的运行工况,并不代表长期。
③辨识性限制。从涡轮流量计内部构造上讲,评估模型只能反映由整流器、涡轮组件、磁敏传感器以及脉冲检测放大电路共同组成的流量传感器的运行工况,它无法辨识涡轮流量计整体计量风险的大小。这就需要涡轮流量计计量风险预警模型来解决。
4.3涡轮流量计计量风险预警模型
①按系统采集的供气绝对压力*高值pmax与qmax乘积大小对涡轮流量计计量风险大小分类。
②建立以监测流量传感器工况为主要目标、温度传感器工况和压力传感器工况为辅助目标的涡轮流量计计量风险预警体系,其基础模型见表2。

预警体系采用人工评估和系统报警相结合的工作方式。其一,由技术人员对流量传感器工况定期评估,根据成绩定性为直观的红、黄、蓝、绿4种状态。其二,技术人员根据季节性气温变化和峰谷供气压力波动,在系统内设定温度和压力报警值,报警值设定后系统自动超限报警。因此,温、压传感器工况有红、绿两种状态,对应非正常和正常状态。其三,当温、压传感器工况都为绿色状态时,该流量计整体工况状态由流量传感器工况颜色决定,必然为红、黄、蓝、绿中的一种。此时,我们可以根据各台流量计各自的流量传感器工况颜色,选择不同的应对措施。当温、压传感器工况二者任意一个超限报警时,该流量计整体工况状态置红(无论该流量传感器工况是何种颜色),提醒我们尽快维修处理故障。实践表明,一个熟练的仪表维修工在停气状态下,更换故障的温度或压力传感器不会超过60min。但是,解决问题的前提是能及时发现问题。否则随着时间的延续,气量损失累积会越来越多,追缴气费的难度会越来越大。这就是建立计量风险预警体系的目的。
③确立报警后的处理等级。涡轮流量计计量风险预警模型按pmaxqmax的大小将客户流量计分为3类,其中A类(重点客户)、B类(主要客户)两类为重点监测项目,要求处理等级与信息反馈速度比C类(普通客户)高。这种分类方法突出了计量管理重点,确立了调配有限资源的指导方针。
表3是建立涡轮流量计计量风险预警系统后,得到的部分涡轮流量计计量风险预警信息。
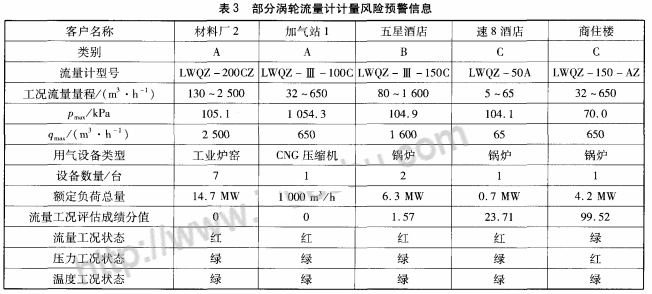
5、工况差的流量计分析
5.1流量计选型
①流量计选型过大
实例用户:加气站1。属A类用户,本次流量工况评估成绩为0分,呈红色报警状态。温、压传感器运行工况都为绿色状态,流量计整体工况状态由流量传感器工况红色状态决定。在用涡轮流量计型号为LWQZ-Ⅲ-100C,工况流量测量范围为32~650m³/h,始动流量为6.7m³/h,流量计规格为G400。用气设备为1台CNG压缩机组,0.8MPa进气压力下的额定流量(折算成标准状态)为1000m³/h。
具体表现为(20%~90%)qmax流量区间的频数为0,负荷主要集中在(5%~10%)qmax。
建议加气站1使用LWQZ-Ⅲ-80涡轮流量计(流量计规格为G100、工况流量测量范围为8.0~160m³/h,始动流量为2.4m³/h)计量,比G400的涡轮流量计更为准确。
②罗茨流量计的选用
实例用户:速8酒店。用户分类为C,本次流量传感器运行工况评估成绩为23.71分,呈红色报警状态。温、压传感器运行工况都为绿色状态,流量计整体工况状态由流量传感器工况红色状态决定。在用涡轮流量计型号为LWQZ-50A,工况流量测量范围为5~65m³/h,始动流量为1.3m³/h,流量计规格为G40。用气设备为1台额定热功率为0.7MW的常压热水锅炉。
该用户用气流量主要集中在设计*大流量的20%以下和90%以上,两*流量用时长,并有过载现象发生。针对此类用气负荷,仪表选型应优先考虑罗茨流量计。例如,流量计规格为G65、量程比为1∶160、始动流量为0.05m³/h的罗茨流量计。
事实上,近年来国内同行针对中小工商用户多变的用气负荷,在推广使用规格为G16~G65的罗茨流量计的实践中,获得了良好的成效。
5.2计量方式
本文所说的计量方式,是指对多个设备用气进行总表计量或分表计量的方式。当设备用气量受诸多因素影响变化较大时,宜选择分表计量方式。
实例用户:材料厂2。属A类用户,本次流量传感器工况评估成绩为0分,为红色报警状态。温压传感器运行工况都为绿色正常状态,流量计整体工况状态由流量传感器工况红色状态决定。在用流量计型号为LWQZ-200CZ,工况流量测量范围为130~2500m³/h,始动流量为20.0m³/h,流量计规格为G1600。用气设备为7台(额定热功率总量为14.7MW)工业炉窑生产线。
笔者在用户走访中了解到,材料厂2是生产稀土的民营企业。由于在生产过程中要排放大量的工业废物,2011年该厂迫于当地环保的压力,不得不降低产量而只开1条生产线。这样,用气负荷几乎全部集中在流量计(5%~10%)qmax区间内,势必造成较大的计量误差。
总表计量问题同样出现在B类用户五星酒店锅炉房。1台型号为LWQZ-Ⅲ-150C涡轮流量计负责两台蒸汽锅炉(3.15MW/台)用气计量。据酒店工程部经理介绍,两台锅炉一开一备,1号锅炉为备用炉,只在2号锅炉检修时才启用。这台涡轮流量计按两台锅炉负荷选型,实际上却计量了一台锅炉用气。
因此,对于额定热功率在0.7MW以上的锅炉以及工业炉窑生产线,如果条件允许,尽可能分表计量,以确保小流量时的计量精度。当用户现场环境难以满足分表计量条件时,应尝试计量创新,例如可选用宽量程气体计量装置等。
5.3计量故障
①故障现象描述
用户商住楼属C类用户,本次流量传感器工况评估成绩达99.52分,为绿色状态,温度传感器运行工况也为绿色状态,但压力传感器有故障呈红色报警,因此,该流量计整体工况状态为红色状态。压力值始终显示为70kPa。
在用涡轮流量计型号为LWQZ-150-AZ,工况流量测量范围32~650m³/h,始动流量为7.8m³/h,流量计规格为G400。用气设备为1台4.2MW常压热水锅炉,负责商住楼冬季供暖。监测系统报警后,笔者在现场确认报警属实,修正仪绝对压力恒定显示为70kPa。现场观察与其同进气管道的其他流量计修正仪,显示绝对压力在105~107kPa区间波动。
②估算该传感器故障带来的计量损失
为简便计算,正常绝对压力值取下限105kPa。
根据气态方程修正公式有:

式中 qf———压力补偿有误的标准状态流量,m³/h
Zn———标准状态下的气体压缩因子
Zg———工作状态下的气体压缩因子
Tn———标准状态下的温度,K,取293.15K
Tg———被测介质的温度,K
pf———压力传感器故障状态下的绝对压力显示值,kPa
pn———标准状态绝对压力,kPa,取101.325kPa
qg———工况流量,m³/h
当供气压力(表压)小于100kPa时,本例可按AGANX-19计算压缩因子值,取:

则式(2)变形为:

当压力参数为正常状态时,有:

式中 qt———压力参数真实时的标况流量,m³/h
pt———压力传感器正常时压力参数值,kPa
将式(3)代入式(4)并整理,有:

将pt=105kPa和pf=70kPa代入式(5),有:

即在qf=70kPa的故障值下,修正仪对工况流量错误修正,累计标况体积造成的50%的气量损失。如果该锅炉每月用气计量为10×104m³,则真实用气量约为15×104m³。本例是C类用户,对于A、B类用户形势会更为严峻。
同理,对于温度传感器故障,也可以类似估算。
借助于涡轮流量计计量风险预警体系,我们先后发现了多起温压传感器故障,由于处理及时、维修迅速,避免了公司气量损失,并对那些规避计量的用户起到了威慑作用。
6、结论
①建立以流量传感器、温度传感器和压力传感器运行工况为主控对象的涡轮流量计计量风险预警体系,明确计量风险处理等级与信息反馈速度,提高流量计传感器维修及时率。用先进技术手段和管理制度来确保计量仪表的准确计量落在实处。
②做好仪表选型和计量方式选择工作,是保证计量准确度的前提条件。对于中小工商用户设备用气,计量仪表选型时应坚持罗茨流量计优先原则;对于0.7MW以上的锅炉以及工业炉窑生产线等用气设备,因受诸多因素影响,用气量变化较大,必须坚持分表计量原则;分表计量条件受限制时,应坚持计量创新原则,拓展新的计量方式或试用新型计量仪表。
相关资讯
- 气体涡轮流量计安装直管段要求
- 气体涡轮流量计的结构与工作原理
- 气体涡轮流量计的产品特点和适用范围
- 气体涡轮流量计选型指南与外形尺寸
- 涡轮流量计的常见故障及排除
- 涡轮流量表怎么调节
- 涡轮流量计安装直管段要求
- 涡轮流量计的适用场合与量程范围
- 涡轮流量计由什么组成
- 涡轮流量计的工作原理
- 压力对涡轮流量计精度的影响
- 液体涡轮流量计使用常见问题
- 液体涡轮流量计的使用场合
- 液体涡轮流量计怎么接电
- 涡轮流量计的使用范围
- 涡轮流量计安装条件与环境要求
- 涡轮流量计安装在什么位置
- 液体涡轮流量计设置方法
- 气体涡轮流量计使用环境
- 气体涡轮流量计使用注意事项
- 气体涡轮流量计怎么清洗
- 气体涡轮流量计适用范围
- 气体涡轮流量计为什么要加油
- 气体涡轮流量计波动大解决办法
- 气体涡轮流量计安装距离要求
- 气体涡轮流量计安装注意事项
- 气体涡轮流量计应用范围
- 气体涡轮流量计常见故障有哪些
- 提高气体涡轮流量计精度的方法
- 气体涡轮流量计精度等级